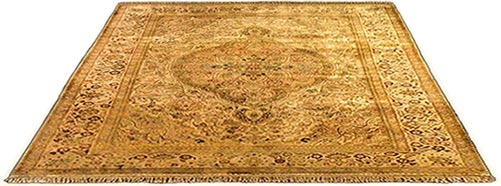 About Handmade Oriental Area
Rugs AN INTRODUCTION FOR THE CONSUMER
Historical Perspective
Introducing you to the exciting world of handmade Oriental area rugs - a world of
timeless beauty and cultural mystique that has remained virtually unchanged for centuries.
The information offered here provides the reader with both a general understanding of the
origin and the creation of an Oriental rug, as well as some of the advantages of including
these handcrafted rugs in your decorating plans for your home, office, or wherever a floor
covering is needed.
While a variety of weavings are mentioned in ancient writings, the origin of handwoven
Oriental rugs is uncertain. The earliest surviving piece, known as the Pazyryk carpet,
dates back to about 400-500 B.C. Discovered in a burial site excavated in southern
Siberia in 1947-49, it is now part of the Hermitage Museum Collection in Leningrad.
Dramatic changes have occurred in today's handmade Oriental carpet industry. Although
weaving techniques and traditions have remained virtually unchanged, the weavers have
found it more advantageous to adapt designs and colors to better satisfy Western decorative
tastes. Moreover, throughout the 1980s, the production of Persian-design carpets in
other countries, particularly India, China, Pakistan, and Rumania has increased significantly,
offering consumers an ever-wider range of color and design choices available in a
full range of prices.
Defining Terms
What exactly is an Oriental rug? As defined by the
Oriental Rug Importers Association, Inc., an Oriental rug is:
- . . .
handmade of natural fibers (most commonly wool or silk), with a pile woven on a warp and
weft, with individual character and design made in the Near East, Middle East, Far East,
or the Balkans.
An Oriental rug is handwoven and varies in quality. Quality is generally determined by
the wool, intricacy of design, and knot density. Wool quality is defined by the length of
its fibers, springiness, and luster. Today, the wool used in handknotted Oriental rugs
either originates exclusively from the country of origin or is a blend of indigenous and
imported wool. Intricacy of design refers to the degree of detail a design possesses as well
as to the number of different colors needed to execute the pattern. The more complex the
design, the more experienced the craftsman must be to weave the pattern. Finally, knot
density and fineness of weave are synonymous. The more knots tied per square inch, the
finer the detail in the design and the more labor-intensive the production.
While machine-made carpets are manufactured to machine-like tolerances, handmade
rugs reflect the human element — the individual's own interpretation of color and design —
which is the essence of their beauty and singularity. Nejad invites you to discover the
fascinating, exotic world of Oriental rugs and to see for yourself
how their use enriches your living environment.
The Fundamentals of Rug Making
Although some of the special techniques involved in weaving an Oriental rug may vary
from country to country and even from one region to another, the principles of rug-making —
from dyeing the yarn to shearing the finished piece — are virtually the same
throughout the world and have changed very little over the centuries. Still, a basic
understanding of an Oriental rug's construction will be invaluable to you when selecting
an Oriental rug.
By and large, most Oriental rugs feature a wool pile, mainly derived from sheep, whose
quality depends on factors such as the animal's breed and diet, local climate, and shearing
season. After shearing, the wool is washed, carded (i.e., a teasing process that straightens
the fibers), and then hand - or machine - spun into yarn. Next, the yarn is dyed in an
attractive range of colors and then dried slowly in the sun.
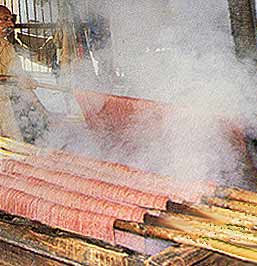 |
| 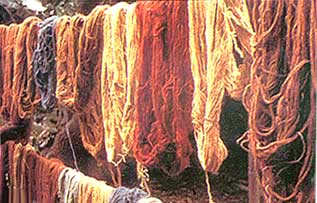 |
After the wool has been spun into yarn it is dyed. | | After being dyed,
the yarn is dried slowly in the sun. |
A detailed illustration of the carpet design, most commonly called a cartoon, guides the
weavers throughout the entire rug-making process. The design is rendered on graph paper
to scale.
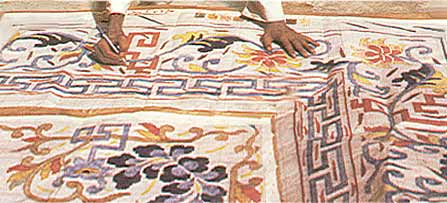 |
A detailed drawing of the carpet's design, which has been rendered to scale
on graph paper, is the weaver's guide throughout the entire weaving process.
|
Through the ages, looms have remained relatively unchanged. While the most primitive
is the nomadic or horizontal loom, the type most generally used today consists of two
vertical beams of either wood or metal and two similarly made horizontal beams. The
distance between the vertical beams determines the rug's width. Warp threads, usually
cotton, are strung between the horizontal beams at a consistent tension. The thickness of
the warp threads and the closeness at which they are strung are two of the elements that
will determine the fineness of the weave (i.e., knot density) of the carpet that is
ultimately woven.
Turkish/ Symmetrical Knot |
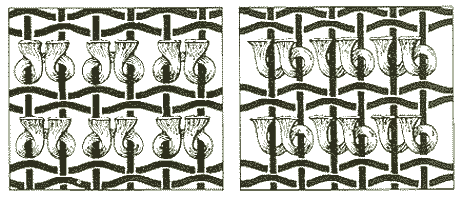 |
Persian/ Asymmetrical Knot |
There are two types of knots used in rug-weaving: the Turkish knot (also called Ghiordes
or symmetrical knot) and the Persian knot (also known as Senneh or asymmetrical knot).
With the average weaver able to tie 10,000 to 14,000 Turkish or Persian knots a day,
several weavers working together can only complete one or two inches of the carpet a
day.
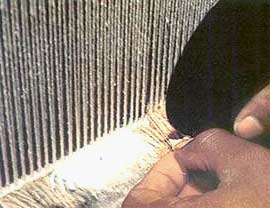 |
|  |
The weaver ties a knot around two adjacent
warps, slides it down to the base of the weft
and cuts the yarn with a knife. | | This procedure of
tying and cutting creates the pile of the rug. |
Before the actual knotting of the pile begins, the rug is secured at the bottom of the loom
by a short kilim, a flat pileless fabric, which is woven by passing several rows of
horizontal cotton threads, or wefts, through alternate warp threads. After rolling the
different-colored yarns to be used into balls, the weaver, reading the design from the
cartoon begins weaving the rug. With the appropriate color yarn, the weaver ties a knot
around two adjacent warps, slides the knot down to the base of the weft, and then cuts the
yarn with a knife, thereby producing the pile. After each row of knots is completed, one
or more weft threads are inserted to secure the knots and are beaten down tightly with a
comb. At this stage, the pile ends are often cut level with a pair of shears. The alternation
of wefts with rows of tied knots is repeated until the carpet is finished. Before removing
the rug from the loom, another kilim is woven at the top. The fringe is formed by the
cutting of the warps at both ends of the rug.
After the rug has been cut off the loom, the final finishing steps take place. First, the
selvedge edges (i.e., side edges of the rug formed by the continuous weft) are bound
or overcast with yarn to reinforce the side edges of the rug. Next, the warp
ends, which secured the rug to the loom, are knotted or braided to form the rug's
fringe. The rug is then washed either by hand or by machine to eliminate dust
and dirt that accumulated during weaving. In addition to cleaning the rug, the
type of wash given the rug can also impart an exquisite sheen and luster to the
wool as well as soften or antique the rug's colors.
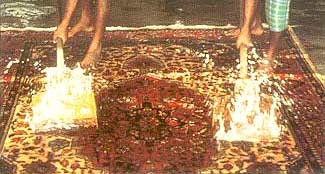 |
| 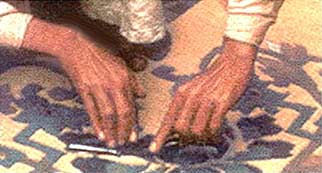 |
After the side edges of the rug are overcast and the fringe has been
knotted the rug is washed. | | On certain carpets motifs are accented by carving or incising. |
Once the rug is washed and dried, a carpet cutter shears the tops of the knots to
create a uniform pile height. In addition to the surface shearing certain carpets
feature carved or incised designs which highlight various motifs. Today, this
type of accenting is often done to Chinese, Indian, and Turkish carpets. The
Oriental rug is now completed and ready for shipment.
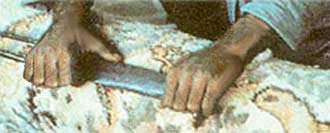
Once
the weaving has been completed the rug is cut from the loom and the surface is sheared to create a
uniform pile height.
|